Should you care about RTLS in warehousing?
With the emerging digitalization, Industry 4.0 and Smart Warehousing, RTLS (Real-Time Location System) applications have gained momentum. Today, you hear the terms digital twins, IoT, IIoT, and even industrial metaverse in relation to warehousing.
What is RTLS? How RTLS applications are utilized today? Which are the benefits of RTLS in warehousing? Is RTLS about digitalization, Industry 4.0 or Smart Warehousing?
Should you care about RTLS?
Some answers to these questions and few insights about RTLS found from this article.
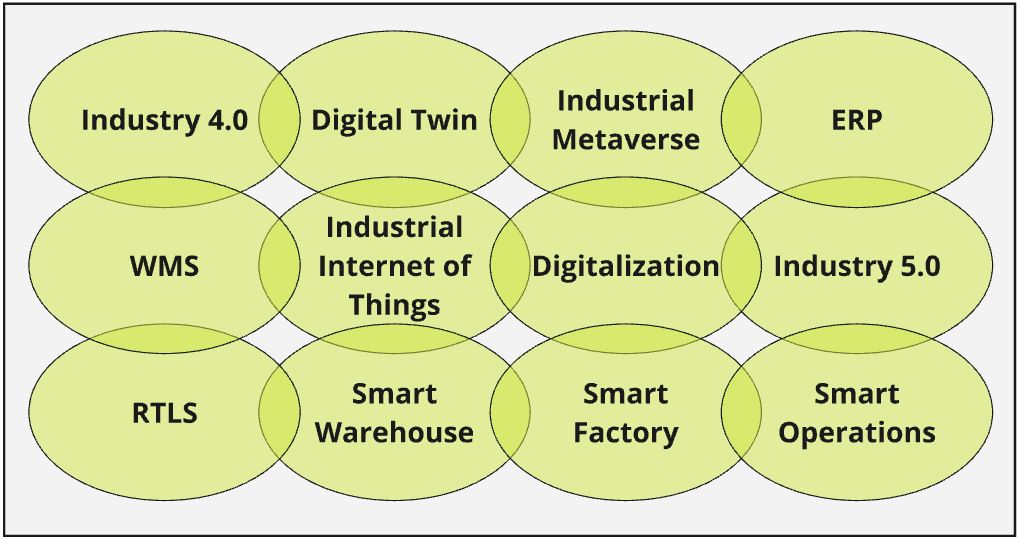
What is RTLS
RTLS (Real-Time Location System) is an application to identify, locate and track assets in real-time. These assets could be e.g. objects or people. The application is built for certain space, and consists of tags, sensors, network and software. The tags are small items attached to assets, from the size of a credit card to a small cup of coffee. The sensors, or beacons or anchors, are attached (fixed locations) to walls or ceiling in the space, and these sensors can locate the tags inside the space. Typically, more than one sensor is connected to one tag to accurately calculate the position of the tag. Triangulation is used in many cases, where three sensors are connected to certain tag. Network is needed for the RTLS, and for the communication, which could be the same network.
The system can identify, locate and track the tags in real time, depending on the latency of the system, and the frequency of the impulses (e.g. every one second update from the tag). RTLS can be built with different technologies, e.g. with UWB (Ultra-wideband), wi-fi, BLE (Bluetooth Low Energy), RFID (Radio Frequency Identification), GPS or computer vision. There are other technologies as well, and the selection of the technology depends on the demands for the application / business case. The technologies differ a lot, especially in the distance of the signal and the accuracy of the positioning, which are the key elements of RTLS. These technologies (and others) can be used also as a combination, forming a RTLS from different technologies. Some business cases might be complex or demanding, where multiple technologies must be combined.
Beyond RTLS
With the emerging drivers like Industry 4.0, Smart Warehousing, and the generic digitalization, we are now seeing more and more IoT (Internet of Things) or telematics utilized in these RTLS systems, on top of location information. Some examples are product status information (temperature, humidity, acceleration) and dynamic asset status information (speed, acceleration, condition, proximity, load status). The other added aspect is system integration, where we are seeing more and more integrations with ERP, WMS, MES and other operative or business systems. And this is absolutely needed, we cannot make valuable findings or analyzes without additional business information.
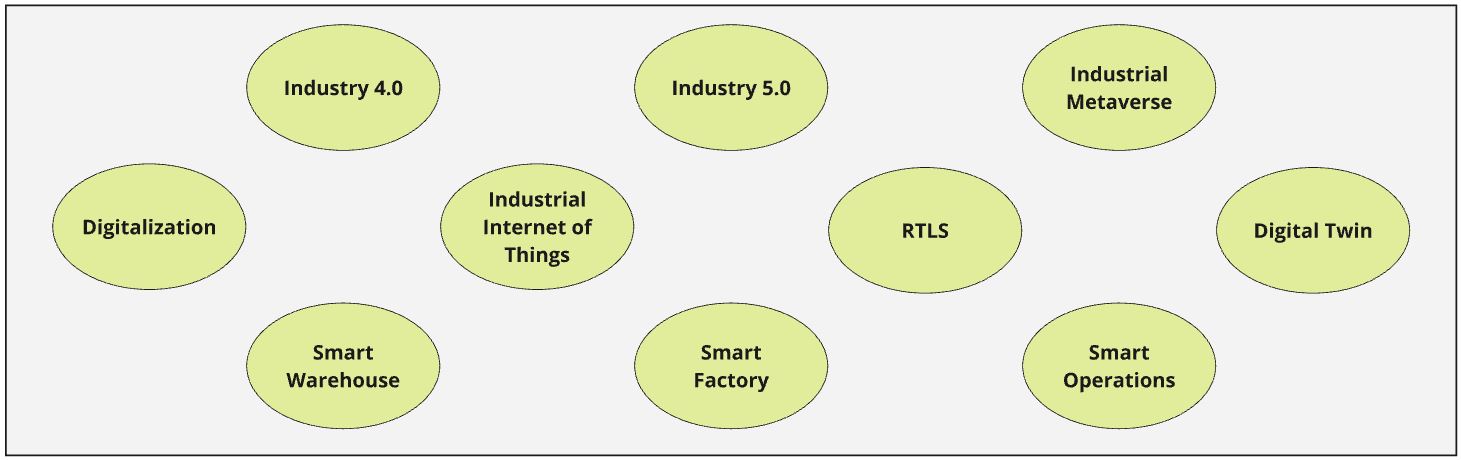
Today, RTLS
applications seems to be "extended" versions of traditional RTLS, where they can
perform real-time monitoring or even controlling, instead of just offering
location information. I see this interesting, as the real-time demands and
requirements are constantly increasing. At some point, only monitoring is not enough,
and responsive solutions and systems will be needed. Ultimately, with deeper
cooperation with operative systems like WMS and/or MES, this might lead to
"real-time management system" in operations, and I think the demand is already
there.
RTLS in warehousing
The challenges of modern warehousing are typically related to inefficiencies, quality and safety. Inefficiency can be also associated with space and storage density, and some other aspects, but now, we focus on operative performance, which is the core of daily operations and a main driver for productivity. The quality of operations is the backbone for warehousing, and this can be dramatically influenced by the systems and processes used. Safety of the operations is the most important element, and it has been typically influenced by the management & culture. However, with modern digital tools, like RTLS, this can be taken to new heights.
Is RTLS useful or beneficial in warehousing? Well, that depends on the problem or challenge you are seeking to solve. I have been telling people, that RTLS is like an X-ray of your operations, it really reveals what is happening in your warehouse. And it gives you a new perspective, information, you were not aware of. However, I do not believe, that only having this picture or information, creates any value for your operations. You have to analyze that, and sometimes additional data is needed. In this context, RTLS-providers have already offered additional telematics from the operations, which is beneficial. But this is still not enough. Typically, you must execute the improvements or developments based on these findings to unlock the potential.
So, how to unlock the potential? First, you need to know how you are currently performing. Typically, professional warehouse operators, like distributors and 3PL providers knows this, but industrial players seem to be lost. Measuring your operations is crucial, which is clear for all, but having the right KPI´s or knowing where you are compared to where you should be, is a different story for most. Many warehouses focus on measuring e.g. picking efficiency, which tend to lead to sub-optimization and in many cases, even to efficiency paradox. This paradox is realized, when focusing only to one part of the process, in this case picking, and forgetting the rest (whole process). This leads to situation, where the process before and after the picking becomes even more inefficient, in this case, putaway and consolidation. Typically, when optimizing picking, e.g. the zone picking is used, and you split orders to achieve efficient picking, but later on consolidate these with big effort, which do not show in your metrics. This might cause the paradox, where you harm your overall performance when trying to improve one area.
It is always the case, that you should measure the whole performance, meaning a KPI which is in relation to overall input, e.g. hours spend in the whole warehouse. One practical example is to measure all transactions performed in the warehouse compared to all hours spend (receiving lines + picking lines / all hours). This is easy to split to sections and sub-metrics.
One story is to know how you are performing, like just discussed. The second story is about how should you be performing. It is easy to say, that your operations is so special, or that cannot be compared to others. That is an easy way of escaping from the reality, and usually leads to stagnation. You should always try to improve – be better every day. In this sense, you should always have ambitious targets where to aim. Benchmarking is a useful tool for this, and participating in different forums to meet and discuss with your peers and even competitors.
Now, if you know 1) how you are performing, and 2) how you should be performing, it is much easier to talk about improvements and the potential what you have in your operations. When you have your targets on high-level, you are able to split and bring those close to operations. This could mean e.g. standard times for different picking types (seconds / pallet pick, seconds / small item pick). In this way, you are able to see deviations and study why these happen. Usually, you can do this with your ERP or WMS. However, that is pretty much the end of it, the seconds per transaction. Having the seconds and transactions can only tell how you are performing against "current operative model". What about if you could know, what are "inside" these seconds and transactions?
RTLS & IoT might have some answers to this. RTLS with added telematics could provide information on the meters driven by certain forklift, are the forklift loaded or not, how fast the forklifts are driving or where the forklifts are moving during the day. With this kind of information, you can really start asking interesting questions like:
- Why are forklifts not driving full speed in main aisles? Why so many turns when driving? Is there something wrong with the lay out, putaway or picking strategy?
- Why forklifts constantly drive long distances to pick items, is the putaway or picking strategy working at all?
- Why are forklifts driving without a load 55 % of the time?
- Why the forklifts are driving too long distances in multipicking, is the routing optimized?
- Why are forklifts driving 156 meters on average per pick? Is the ABC / XYZ working? A standard for e.g. of 90 meters could be calculated and set for operations
- Why maximum of 84 % of the forklifts are utilized during the days, some of the forklift leasing-contracts could be eliminated
- Why there were 4 near misses between a forklift and a person last month, a collision avoidance could be deployed in RTLS
By tagging the pallet, containers, or other handling units, you are also able to locate your products, or monitor the status, e.g. temperature or humidity. This might sound a simple task to just locate your materials, but in many sites, this is a major problem.
By deploying RTLS, this could enable one big leap in digitalization as well, creating a digital twin of your warehouse, whether in 2D or 3D. That would give new tools in planning, simulating and developing your lay out, material flow, product locations and operations. And HSE people (Health, Safety and Environment) have found this beneficial – you basically have a digital twin of your operations, where you can set digital alerts when two assets are closing each other's too fast, or assets are entering the areas where they shouldn´t be.
Like
mentioned, just seeing these fancy digital twins or tons of data, doesn´t
really help you unless you act on it. Now, you would have a lot of new data, this
is where the value is, you just have to start doing these improvements to enjoy
the benefits.
Key takeaways
- RTLS applications identify, locate and track assets in real-time. For RTLS, you need tags, sensors, network and software. Additional telematics (Iot) can be utilized from your operations, and systems can be integrated to this (e.g. ERP or WMS)
- Modern RTLS applications can truly expose your weaknesses in the warehousing operations, and help you to improve the efficiency, quality and safety
- Learn to identify (and build) your performance metrics (KPI´s), know how you are performing, and measure the whole performance of the operations to avoid sub-optimization and efficiency paradox
- Learn to identify how others are performing, and set challenging goals for your operations
- Modern RTLS can reveal you information you were not able to see before, which helps you to identify the improvements and developments at your site. By executing these developments, you will get the results
There are a lot of different elements of IoT, telematics and system integrations involved. Is this now about digitalization? Yes. Is this about Industry 4.0? Yes. Is this about Smart Warehousing? Yes.
Is this then about RTLS anymore? Probably not. Should you care about this? Probably.
I hope this gave some new ideas or insights for you. Please share your thoughts on this!
Janne Kilpua, Logistics Consultant & Doctoral Researcher
https://www.kapitenconsulting.com/en/