Digitalization & Lean in Supply Chain
Digitalization & Lean in Supply Chain: The future of ERP – End of Resource Planning?
From MRP to MRP II, to first stage of ERP´s in the nineties, what´s next?
Industry 4.0 ongoing and companies are struggling what to do with this new era, while Industry 5.0 is already knocking on the door. In this new digital era, what is happening to old & mighty ERP, which used to handle all the corporate functions? Nowadays you hear a lot of these three-letter acronyms like MES, MOM, WMS, TMS, SCM, etc. Where have those come from? And why? And how come those are thriving?
Digitalization
Digitalization has been the very target among several industries and enterprises, though it has not been clearly entered into actual execution at its fullest. Digitalization has a very wide meaning and seems that many enterprises would like to "digitalize" itself, but they have found themselves a bit lost struggling what to do. Many discussions ongoing on the topics like IoT/IIoT and Industry 4.0, but these are wide concepts like digitalization and are yet to be detailed and executed among industries.
Currently there are a lot of challenges working with the constantly changing environment in Supply Chain. The world is changing faster than ever, the customer demands are changing, and the needs are coming faster than ever. This means, that the needs, demands and expectations toward supply chains are getting much higher. Maybe some of the demands have changed over time, and the future might bring some new ones.
Today, companies find it difficult to react fast to the changing environment and adapting their plans. This has led to decreased performance in reliability, lead times and late shipments (responsiveness). The traditional ways of using ERPs in separate or individual departments has worsen the situation, as the real-time big picture has been in the shadows, and the decision making have been really challenging with scattered, limited, and overdue data (situational awareness & decision-making). These factors usually lead to lower performance in delivery capabilities and higher costs. In today´s business, it is clear, that the performance of ERP in supply chains has been crucial, or even game breaking. The increased demand for real-time situational awareness and accurate & swift decision making has absolutely shaped the field. Now, it seems that the traditional ERP has been really challenged.
It is clear, that companies must improve their performance every day, and utilization of digital solutions is a must in a long game in the modern world. Usually, when referring to digitalization and its capability to improve performance, we tend to mean the technical aspect. This is interesting. What if people would be using tools, where the UI would be easy-to-use and software truly engaging? The total performance improvement always needs these two elements - the technical capabilities and the people. Today, we are having a lot of Millennials in our working environment, and Generation Z is making its entrance. Still, many of our IT-systems and UI´s are yet to be modernized. Younger people and these new generations have different needs and expectations, and companies must also consider this aspect – to be an attractive working place and a top-performer in a long run. The people perspective is truly significant, but when looking at Industry 4.0, even paradoxical, it was buried under the machines and automation. Now it seems, that the forgotten perspective will be the foundation for Industry 5.0, literally.
The traditional ERP and the future
The traditional role of ERP has been challenged as the world and the business environment is changing so fast and the needs towards businesses have increased rapidly. On top of this, the needs for changes are coming in much more frequent matter. Traditional ERP´s have difficulties adapting the processes and developing new features. The modern IT-systems should be agile & flexible, which could be adapted much faster to the changed needs.
Some companies have already started the path for changes and implemented new kind of business-digital architectures. One of the main drivers have been the increased amount of information and automation needed inside the operations. And as the demands from the stake holders are increasing with the sense of urgency, this will truly challenge the ERP´s in the coming years. So, what will happen to the traditional ERPs with these new changes? This is hard to say, but some scenarios can be formulated based on these new needs and demands. Below one scenario for traditional ERP in a timeframe, where the increase of automation, information and a need for responsiveness is shown.
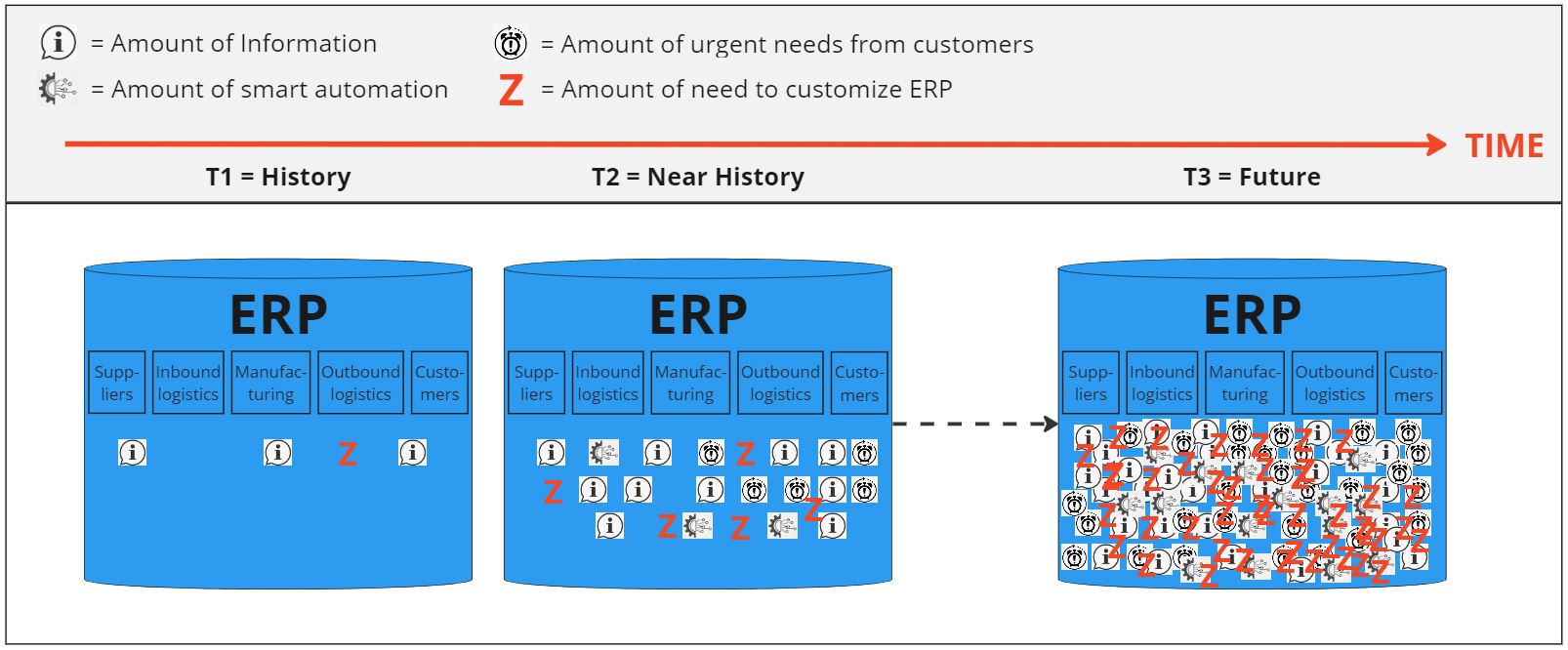
Picture 1. Traditional ERP: one simulated scenario
As shown above, the amount of increased information, automation and needs is substantial, and the ERP must cope with these changes. In the picture, the need for customization is demonstrated with a letter Z, and this shows the need for changes & customizations. Sure, this whole equation depends on your business, but in this scenario is shown a visual example of one simulated scenario.
ERP - Future scenarios
So, what to do? Sure, there is no simple answer, as the future is uncertain, and your business size & characteristics defines your situation & needs. However, some future-scenarios can be formulated based on the issue presented above. Below is demonstrated the situation in Picture 1, with some alternative options to go forward:
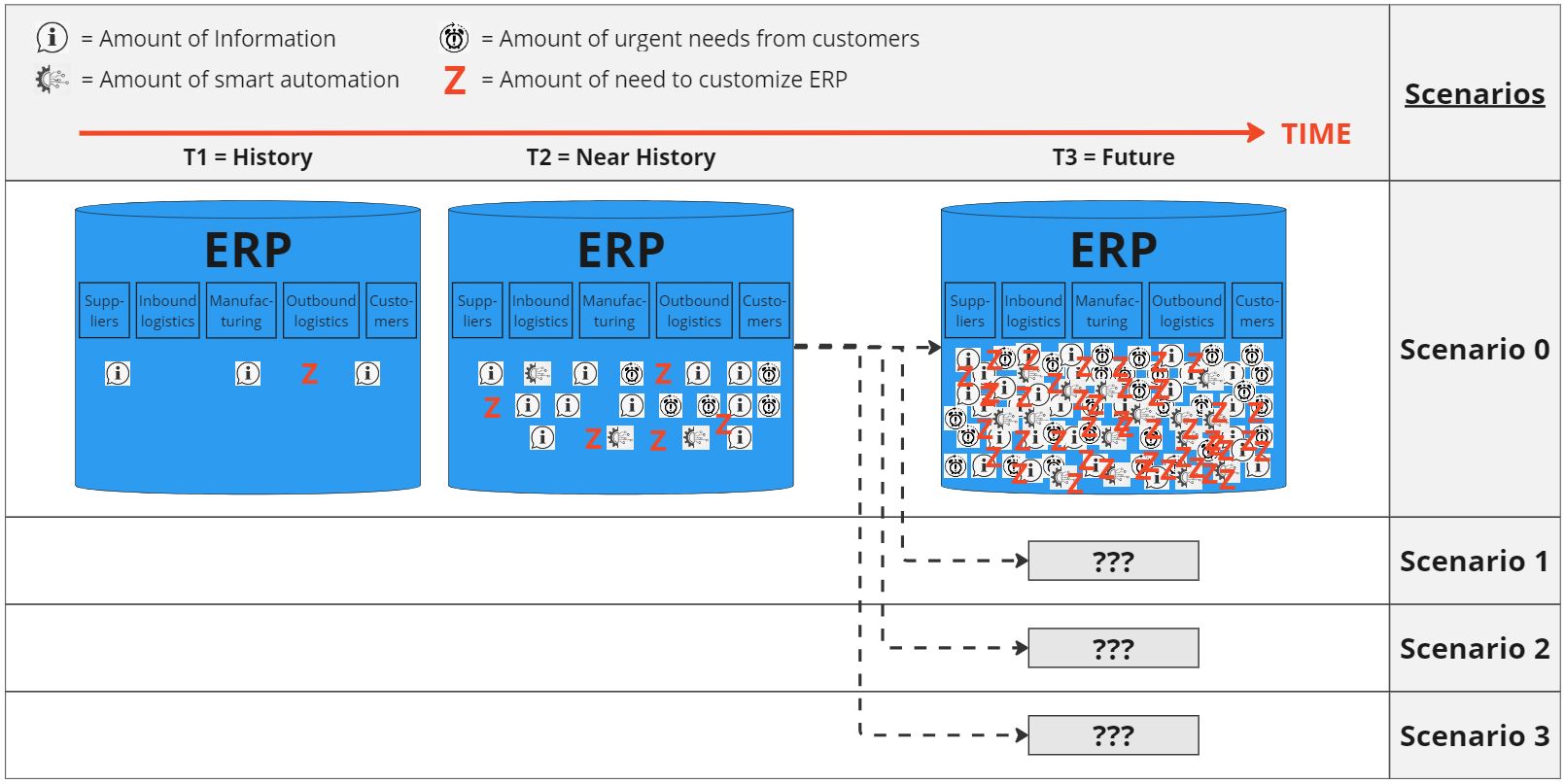
Picture 2. A fork in the road
As we can see from the picture above, this would be a decisive moment or a fork in the road – to continue with the current path or doing something different. Below presented these alternative scenarios on high-level for the future ERP in the context of supply chain:

Picture 3. Simulated future scenarios of ERP
Scenario 0
Traditionally, companies have selected the centralized system strategy, which means that the ERP is utilized in most of the operations. In global manufacturing companies this means that all processes are harmonized globally, and the operations are standardized. The centralized strategy targets to have cost-benefits by having only one set of processes (cost-centric strategy). By operating this harmonized way, the running and developing processes would bring synergies, as there is only one set of processes. The downside has usually been, that by having only one set of processes, the local fit has not been perfect. This means, that the local businesses need to adapt to the global processes. Too often, unfortunately, this leads to lower performance in the traditional KPI metrics locally.
However, selecting the strategy does not solely mean whether the company will be successfully or not, the execution of the strategy defines the results. It is, indeed, the execution of the strategy, which has been the pain point in this case. In these cases of centralized strategy, in many cases, the execution has been undisciplined, which have led to poor results in achieving cost-benefits. In the worst case, the company has not been able to harmonize the processes globally, and the process-setup has become scattered. This means, that the company is not able to get cost-savings nor the local performance.
With the increasing amount of information, automation and the needs & urgency, this strategy will be challenged strongly in the coming years. This means, that the local performance is even harder to maintain, and global harmonization will be very tough. In this scenario, it will be much more challenging to realize the benefits of the strategy in the future. With the speed of these changes coming, it might be very difficult to cope with the changes in ERP in the future.
Scenario 1
Some companies have found the Scenario 0 strategy too costly, time-consuming, and having a system in different sites which cannot handle the local needs. The Scenario 0 ERP, and the resources needed to maintain it, tends to be extremely "heavy", with missing flexibility and agility. These are some of the drivers for the Scenario 1, which is a kind of Laissez-Faire, where every location can choose the best possible solution for their needs. Sure, there might be some challenges in integrating these Tier 2 ERP´s to Tier 1, but the local business benefits are undisputable. The scenario would also allow sub-systems under the Tier 2 ERP, which would even strengthen the local position.
Scenario 2
The target for this scenario is, that ERP is absolutely standardized, and the scope of ERP has been decreased compared to Scenario 0. This means that the reduced scope from ERP has been moved to sub-systems. In this case, there are agile and flexible systems under ERP, which can be adjusted to changes when needed. Usually in these systems, the lead time for developments is rather short, and the system-architecture allows much more customization. Normally, even the standard-level is pretty impressive, as these systems are built for specific usage and operation. This means, that years of expertise, lessons learned, and best-practises, are already build into the system. From strategic point of view, traditionally, this would mean focusing only to local business performance (differentiation strategy) and the cost would not be the driver.
However, in the recent years with more sophisticated sub-systems, the "hybrid" strategy has been rising in global scale. In this hybrid strategy, the target is to have standardized ERP, and also, modular-structured sub-systems, which could be even referred as standardized ones. This would enable win-win outcome regarding cost-benefits and local performance if you are able to execute with excellence.
Scenario 3
This could be one of the future scenarios, where all the operations could be managed and controlled by one sophisticated system. In the coming years, there will be much more smart automation integrated to processes and there will be a need to manage and control this infrastructure from one system or control tower. This could be connected to ERP in a way, that the system is able to visualize all the operations to one single digital platform, where the decision making, management and control would happen. This would mean integration also horizontally and vertically downwards.
Some additional drivers for this scenario might be some pitfalls in Scenario 2. When having one dedicated system operating in one field of the operations, sure, it is the fit for the purpose. This also means, that the scope of the system is limited, and the system is not aware what is happening in the whole process. This might mean, that the system is performing absolutely great, but still, the operations are limping. It is crucial to manage and control the big picture (situational awareness) to optimize the total outcome. Maybe the article below demonstrates the problem:
https://www.linkedin.com/pulse/warehouse-management-wms-vs-erp-elephant-room-janne-kilpua-kdfcf%3FtrackingId=%252BHdx1ep%252FRaSH%252F8DXY8OtUQ%253D%253D/?trackingId=%2BHdx1ep%2FRaSH%2F8DXY8OtUQ%3D%3D
Why the need for change is inevitable?
- Situational awareness. To know what is happening in your operations, you have to have all the knowledge on your hands, from big picture to details. In the modern world, this means having digital dashboards or virtual platform, where you see the complete status of your operations.
- Real-time responsiveness & decision making. With the increasing amount of information, automation, and needs & urgency, you must make accurate decisions faster and faster. This means that the need for real-time data is crucial, and the systems need to provide this in a sophisticated manner. Traditionally, ERP´s have been working on daily level, and unfortunately, this is not enough anymore. The need for the operative systems to react, have changed dramatically from hours to minutes and to seconds.
- Delivery capabilities. With the improvements above, you are able to increase the performance of your delivery capabilities. This means having more reliable operations with better quality, shorter lead times, faster and punctual deliveries. With the changes, your responsiveness increases dramatically, which means being real-time aware of the outstanding issues and responding to those. That might mean reacting to missing resources, parts, or supplier deliveries before those can harm the operations. Basically, you would be "on top of things", where you can react to issues before they occur. In the end of the day, these elements would give you a competitive advantage and satisfied Customers.
- Costs. When you have the situational awareness, you are able to Lean your concept & operations and reduce waste. This might even mean rebuilding your processes. With Lean, and increased delivery capabilities, there is a significant potential to achieve cost savings.
Key takeaways:
- With the constantly changing business environment, identify the need for review of your supply chain IT-strategy - if you are not working on these topics, your competitors probably are
- Execute an objective analysis of the current state of your supply chain operations, make sure your team has truly diverse expertise and you are honest to yourself
- Make sure, that you are aware of the digital tools available. Maybe a good time to review that you have the right kind of knowledge & competence available for the future possibilities
- Digitalization is here to stay, do not try to deny this and start to get onboarded
- Make your best analysing the future business and modifying the strategy. You can actually make changes! What got you here, won´t get you there!
I hope this gave some new ideas or insights for you. Please share your thoughts on this!
Janne Kilpua, Logistics Consultant