Digitalization & Lean in Warehousing
Warehouse Management: WMS vs. ERP and the elephant in the room. Change your focus from single transaction to whole process, visualize your operations & supply chain and re-build your concept.
Last fifteen years I have been involved with the topics and projects in this field, and I wanted to share some thoughts on this. During the years, I have noticed that this subject is rather debated and a lot of opinions and even strong feelings regarding the matter. In this article, my perspective is mainly warehouse operations after go-live and operations development. In this context, the ERP is considered as a major ERP-provider globally. During the years, I have led several system-implementations to warehouses, and both ones, ERP-project and WMS-project. From these experiences, I have summarized some characteristics between these two systems:
Warehouse Management: Empirical experiences on ERP vs. WMS
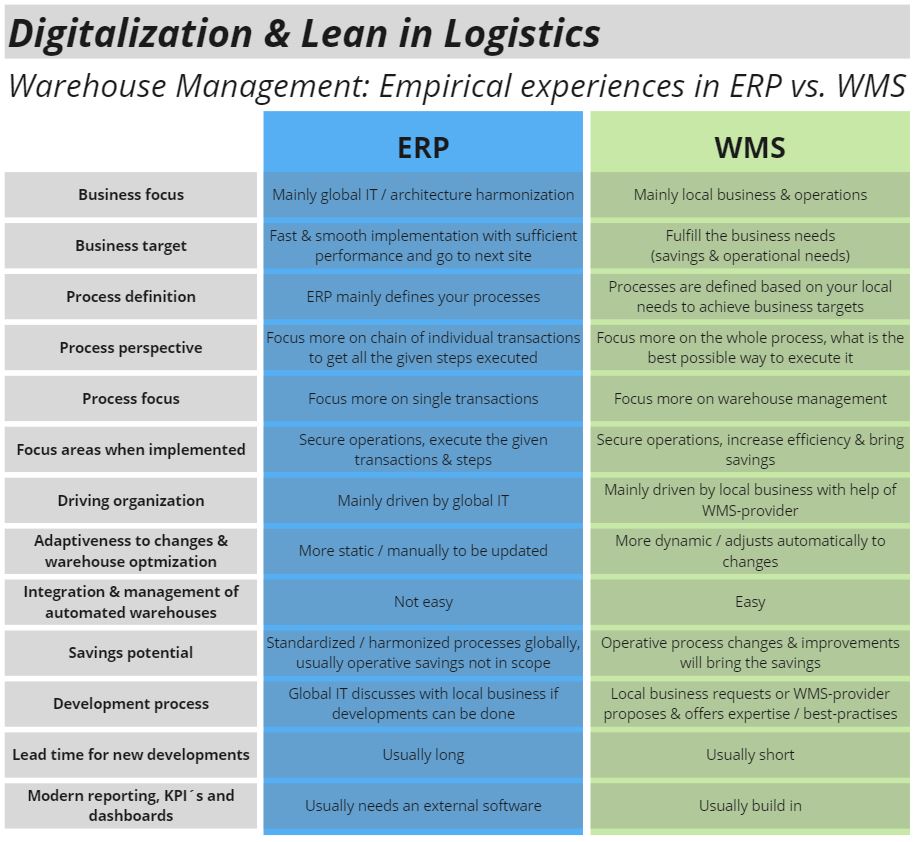
As shown above, WMS tends to have a wider perspective on processes & management and a local business to focus on. The actual savings rarely comes from doing one transaction a bit faster, the savings comes from re-defining and streamlining (Lean) the processes during the project. To achieve this, you really need a wider view on the processes and a mentality to questions the old way of doing things. When executing the process re-definition, Lean must be the philosophy and flow as the guiding principle.
In ERP environment the focus tends to be more on single transactions. The focus is to execute all needed steps, and later in developing the system, how to execute one transaction faster in a chain of transactions. This might originate from the process definition, where the ERP usually defines your processes. Following this logic, it is logical to optimize the transactions on your second step. However, usually when analysing or optimizing one single transaction or task, you might lose the big picture - what is really happening at your operations. In this case, you would be optimizing one single resource, and this easily leads to sub-optimizing and might hurt the process before, after, or some other process in operations. In this case, the guiding principle would be resource optimization in single transactions, which is almost a contrary to flow.
Flow and resource optimization
This distinction between these two guiding principles, flow and resource utilization / optimization, is really interesting. (Book recommendation: Niklas Modig: This is Lean – Resolving the efficiency paradox). The main principle for Lean is the flow, and this should be always followed if Lean is your target state. In my experience in manufacturing industry, Lean is usually something companies wants to do, but many times it is not actually happening in supply chains or in warehouses. Why is this?
One of the problems in manufacturing industry regarding missing Lean might be, that the companies are not aware of the reality on shop-floor. I have been working in several positions in distribution, retail businesses and in manufacturing industry. Is it clear that distribution and retail are way ahead of the manufacturing industry, and this is clear – there is no business in retail / distribution if you don´t have a cost-effective supply chain with reasonable service level. In distribution / retail, Lean is usually present, and flow is the guiding principle. Actually, this is a must in distribution / retail business with high volumes - you can not allow any blocks to the flow, otherwise your operations will be stopped in short time. In manufacturing industry, the story is a bit different. In manufacturing industry, there is no absolute force to push companies to make thing better. Many times, the change happen, when there is no other way than to change. This might come from the business itself - the gross margins of the products in manufacturing industry are way higher than in distribution business. This might mean, that the driving force is missing, and companies are leaving a lot of money to the table.
The other reason of missing Lean (and flow) in manufacturing industry might be the legacy. The history itself has been highlighting the importance & focus on machines and production. From the management point of view, traditionally the running of the machines or production lines has been the main focus. In this context, by operating this way, the guiding principle is resource utilization which usually leaves no room for flow. This kind of production-centric view leads easily to minimal attention to other departments, like logistics. And when taking this further, and optimizing the production, this easily leads to sub-optimizing situations, where you might harm the other processes and even add total costs.
ERP & WMS and some questions to ask yourself
Regarding ERP, the main focus tends to be in individual transaction, where WMS focuses on the whole process in the warehouse. In the case of ERP, the main questions should be, that do we even need to perform the transaction at all? With Lean, you should always questions this and find ways to streamline your processes. In ERP, you can endlessly finetune your single transactions, and you might have the best possible transactions, but you still might lack the warehouse management system or the efficient operations. For the guiding principles, beware of the resource utilization in the cost of flow.
In the case of WMS, the focus tends to be on the whole process & warehouse management. In this case your main question should be, that do we even need the materials here in the first place. Re-defining your logistics concept might give some answers to this. This might mean direct deliveries, dropshipping, or having the previous warehouse in your supply chain to ship these. Many times, materials are moved from warehouse to another, and people are doing their jobs, but the concept is limping. For the guiding principles, make sure the flow is present at your site, and widen your Lean-scope to whole supply chain.
The point: Change your focus from single transactions to whole process! And during this exercise you should question & Lean your logistics concept. The best way to approach this is to visualize your daily operations in one (digital) board. And when doing this mapping of operations, go to the shop-floor and you don´t miss any "silent" or "hidden" processes or tasks - the truth is always on the shop-floor. In this exercise you discover what is really happening in the whole process & supply chain; from suppliers to end-customers. I have experienced that most of the times when you are able to visualize what is happening, the usual rection is "that doesn´t make any sense!". This is where the learning and the journey begins!
What do I think?
Regarding do I prefer ERP or WMS in the warehouse management. I think the case is not so black-and-white. Actually, these two systems are not even fighting the same fight. In some cases, ERP is definitely the fit, where some cases WMS is the one. And in most of the cases, these can be combined in a very sophisticated way. Your needs define the needed solutions, and usually that depends on your required processes, volumes, automation involved or the characteristics of the products or warehouse. In this context, it is very crucial to identify two key elements: time and changing environment. The world is changing faster and faster, and the needs from your customers and other stake holders are changing faster than ever. And regarding these needs, the sense of urgency is also increasing, which means your responsiveness needs to improve over time. On top of this, the amount of information and automation are increasing rapidly, which means that our business environment won´t be the same in 5-10 years from now. As these ERP / WMS topics are long-term investments, you should be evaluating your scenarios for the future needs.
Sometimes some distance helps you to see the daily issues, and what is really happening in the operations. Many times, things are done in certain way, because they have been "always" like that. Digitalization is well under way and maybe this would be the time to question your status quo in operations. Nowadays there is a plenty of software & tools available to help you in your journey, you just need to begin!
Key takeaways:
- Shift your focus from individual transactions to the whole process
- Utilize Lean and start question the need of your transactions executed currently
- Focus on the flow in the process (Lean) instead of resource optimization
- Widen your scope to the whole supply chain and use Lean to streamline it from suppliers to end-customers
- Optimize or re-define your supply chain concept for the future and then analyse the digital tools (software) needed – if your concept is limping, there is no software in Hämeenlinna which could save you!
I hope this gave some new ideas or insights for you. Please share your thoughts on this!
Janne Kilpua, Logistics Consultant